- Introduction to woven steel mesh
and its significance - Technical attributes and specific mesh types comparison
- Advantages and material selection for woven wire mesh
- Manufacturers overview and comprehensive comparison
- Tailored solutions and customization opportunities
- Industrial case studies and practical applications
- Conclusion: The enduring value of woven steel mesh
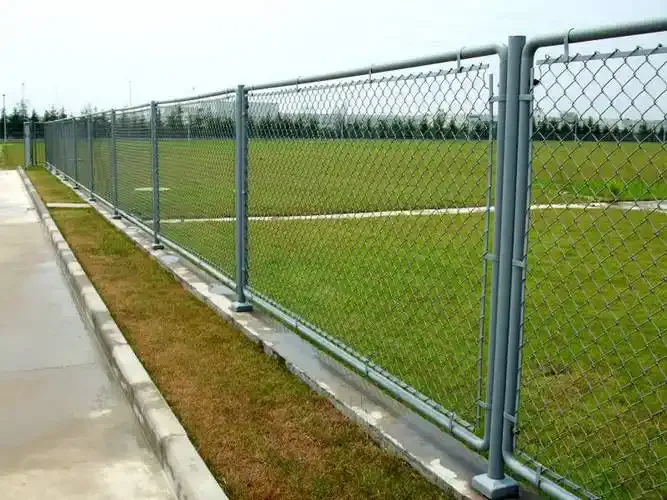
(woven steel mesh)
Exploring the Versatility and Importance of Woven Steel Mesh
Woven steel mesh plays a pivotal role in modern engineering, construction, filtration, and security applications. Defined by its interlaced metallic wires, this mesh structure offers an optimal balance between structural integrity, versatility, and permeability. In industries ranging from chemical processing to architectural design, woven steel mesh is celebrated for its high strength-to-weight ratio and durability under extreme conditions. The global industrial wire mesh market surpassed USD 14 billion in 2022, demonstrating an annual growth rate of 5.8%. Its adoption is expanding rapidly, as more sectors discover the performance, cost, and sustainability benefits it delivers. With continuous innovation, products like 304 stainless steel woven wire 120 mesh, 304 stainless steel woven wire mesh1 roll 5 mesh, and mild steel woven mesh are meeting specialized needs, enabling enhanced filtration, protection, and design capabilities.
Technical Breakdown and Mesh Types: Understanding Your Options
Mesh products are not created equal. Key technical distinctions in wire diameter, aperture size, and alloy composition define their suitability for different tasks. The 304 stainless steel woven wire 120 mesh is engineered for micro-filtration—a weave with 120 openings per inch, offering apertures as fine as 0.125 mm and wire diameters around 0.09 mm. This makes it optimal for high-performance liquid and gas filtration in chemical and food processing sectors.
In contrast, 304 stainless steel woven wire mesh1 roll 5 mesh features a much coarser five-mesh-per-inch pattern, using thicker wires (typically ~1 mm diameter) and larger aperture size (~4.06 mm). This type is favored for screening, architectural panels, and heavy-duty sieving.
On the other hand, mild steel woven mesh is preferred for applications where cost efficiency and moderate corrosion resistance suffice, such as temporary fencing or aggregate separation.
The table below summarizes key specifications:
Mesh Type | Material | Mesh Count (per inch) | Wire Diameter (mm) | Aperture Size (mm) | Corrosion Resistance | Common Usage |
---|---|---|---|---|---|---|
304 SS Woven Wire 120 Mesh | 304 Stainless Steel | 120 | 0.09 | 0.125 | Excellent | Fine filtration, separation |
304 SS Woven Wire Mesh 5 Mesh | 304 Stainless Steel | 5 | 1.00 | 4.06 | Excellent | Screening, security |
Mild Steel Woven Mesh | Low Carbon Steel | 2–20 | 0.5–2.0 | Varied | Moderate | Fencing, sifting aggregates |
Such technical diversity allows users to precisely match mesh characteristics with performance requirements, optimizing both initial investment and long-term operation.
Performance Advantages and Material Selection in Woven Wire Mesh
Woven wire mesh's dominance in industrial applications stems from its blend of mechanical strength, precise control over particle passage, and corrosion resistance. Selecting the correct material is fundamental.
304 stainless steel, an alloy containing approximately 18% chromium and 8% nickel, is recognized for exceptional resistance to rust, chemicals, and high temperatures. Its yield strength averages 215 MPa, and its maximum service temperature exceeds 870°C, making it ideal for aggressive process environments.
Meanwhile, mild steel woven mesh is favored where budget constraints take precedence or where environmental exposure is limited. It provides reliable tensile performance, but it is prone to corrosion if subjected to moisture, unless it is galvanized or coated.
Flexibility is another advantage: woven mesh exhibits effective formability without loss of function, allowing custom shapes and installations across complex geometries. Installation time for standard mesh panels is often 15–30% shorter compared to welded mesh panels, due to their adaptability.
Additionally, woven steel mesh maintains high open-area ratios, which is critical for maximizing throughput in filtration, ventilation, or protective barrier applications.
Manufacturer Comparison: Quality, Innovation, and Global Reach
The selection of global manufacturers significantly influences the performance, delivery timelines, and compliance of woven steel mesh products. Major manufacturers include W.S. Tyler (USA), Boegger Industrial Limited (China), BOPP (Switzerland), Dorstener Wire Tech (Germany), and Locker Group (UK).
Below is a comparative analysis of international leaders:
Manufacturer | Country | Product Range | Lead Time | Customization | Certifications | Market Focus |
---|---|---|---|---|---|---|
W.S. Tyler | USA | Alloys, micron meshes | 2-5 weeks | Advanced | ISO 9001, ASTM | Filtration, Architectural, Mining |
Boegger Industrial | China | Stainless steel & mild steel mesh | 1-3 weeks | Standard/Custom | ISO 9001 | Industrial, Fencing, Agriculture |
BOPP | Switzerland | High-precision fine mesh | 3-5 weeks | Highly Specialized | ISO 9001, ISO 14001 | Pharma, Aerospace |
Dorstener Wire Tech | Germany | Custom, precision meshes | 3-4 weeks | Flexible | ISO 9001 | Automotive, Food Processing |
Locker Group | UK | Woven & welded mesh panels | 2-6 weeks | Standard/Custom | ISO 9001 | Construction, Rail, Oil & Gas |
Key differentiators among these vendors are their delivery timeframes, level of product customization, and certifications. For the most demanding or regulated industries, opt for vendors with ISO 9001 and relevant industry-specific certifications for guaranteed quality assurance.
Customization Pathways: Tailor-Made Mesh Solutions
With the ever-widening span of industrial requirements, standardized woven wire mesh is often insufficient. Manufacturers offer a suite of customized options to address unique operational, design, and regulatory challenges. Customization parameters typically include:
- Mesh count and wire diameter: Dictates the filtering precision, appearance, and tensile capacity. Options range from ultrafine (<10 microns) to large diameter (over 5 mm).
- Material: Beyond 304 stainless steel and mild steel, choices cover alloys such as 316L stainless, Monel, Inconel, and phosphor bronze for enhanced temperature or corrosion resistance.
- Surface finish: Electropolishing, passivation, coating, or painting improves durability and aesthetics.
- Form factor: Supplied as rolls, sheets, or custom-cut shapes, with options for edge treatments, borders, and mounting aids.
- Compliance: Manufacture to global standards (ASTM, DIN, JIS) or custom documentation to meet site-specific regulatory requirements.
Lead times increase with customization, but the operational efficiency gains and risk mitigation far outweigh the additional investment. For example, a pharmaceutical customer’s tailored mesh, produced with electropolished 316L stainless and a bespoke weave density, resulted in a 35% decrease in maintenance hours annually through improved cleanability.
Industrial Applications: Success Stories and Real-World Impact
Woven steel mesh underpins innovation across manufacturing, processing, security, and architecture. The following case scenarios illustrate diverse, high-value applications:
1. Petrochemical Filtration: A Middle Eastern refinery employed 304 stainless steel woven wire 120 mesh dynamically within catalyst bed supports. The mesh’s fine aperture maximized contaminant capture, reducing downstream downtime by 28% compared to legacy filtration substrates.
2. Architectural Screens: An Australian stadium facelift incorporated woven stainless steel mesh (5 mesh per inch) for façade cladding. The solution delivered 80% open area for airflow and shade, while withstanding cyclonic wind loads up to 300 km/h and requiring minimal maintenance over a decade.
3. Milling & Food Processing: European grain processing leaders turned to mild steel woven mesh for primary milling screens. Their material cost savings averaged 22% versus stainless steel, with tailored coatings extending useful lifespan by 18 months on average.
4. Water Treatment: In North America, custom tensioned 304 woven wire panels were used in tertiary filtration stages, achieving a 20% increase in particulate removal efficiency (<20 microns) in a retrofit of municipal waterworks.
These successes highlight not only efficiency and safety improvements but also the value in selecting the right mesh specification for each scenario.
The Future and Enduring Value of Woven Steel Mesh
The demand for woven steel mesh continues to escalate as industries embrace stricter standards and seek robust, sustainable solutions. Current data reflect a 15% year-over-year uptick in complex mesh custom orders, driven by sectors like renewable energy, smart manufacturing, and adaptive urban design.
Ongoing advances in alloy development and computer-aided weaving promise further technical refinements, enabling even tighter tolerances, higher-performance materials, and creative freedom for designers and engineers. As operational lifespans widen and ecological benefits—such as 100% recyclability of stainless meshes—gain prominence, woven steel mesh stands out as an indispensable asset for both new projects and infrastructure upgrades.
For stakeholders prioritizing reliability, performance, and future-proof solutions, woven steel mesh will remain an essential component at the heart of modern progress and innovation.
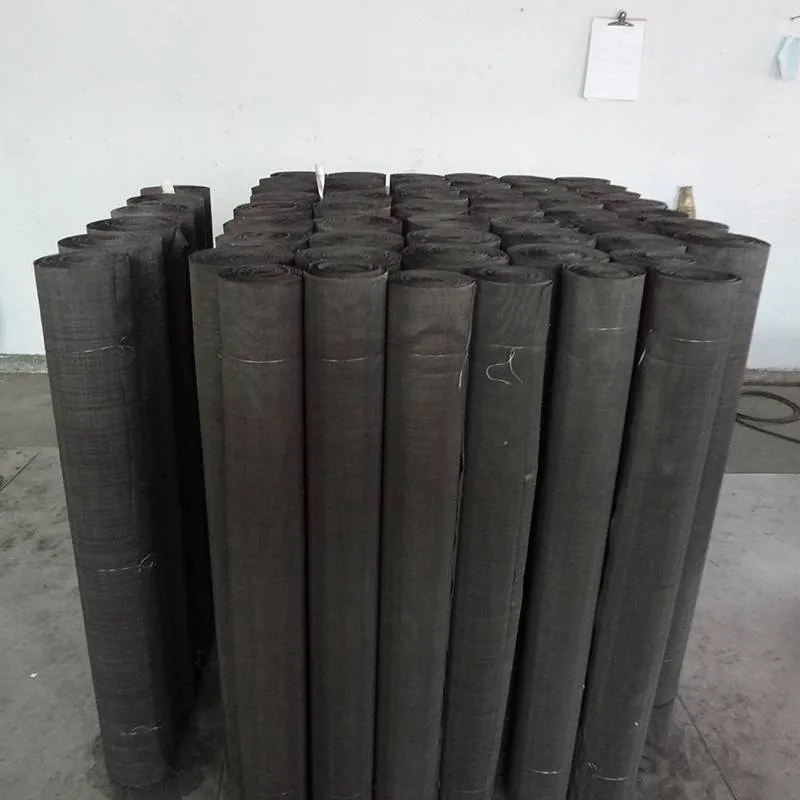
(woven steel mesh)
FAQS on woven steel mesh
Q: What is woven steel mesh used for?
A: Woven steel mesh is commonly used for filtration, sieving, and protective barriers. Its strength and flexibility make it ideal for industrial, architectural, and agricultural applications.Q: What makes 304 stainless steel woven wire 120 mesh special?
A: 304 stainless steel woven wire 120 mesh offers excellent corrosion resistance and fine filtration due to its high mesh count. It's widely used in chemical processing and food industries.Q: How is the "304 stainless steel woven wire mesh 1 roll 5 mesh" labeled?
A: This label means the roll contains woven mesh made of 304 stainless steel with five openings per linear inch. It's suitable for coarse filtration and screening applications.Q: What are the advantages of mild steel woven mesh?
A: Mild steel woven mesh is cost-effective, easy to form, and provides good strength for general purpose uses. It's often chosen for fencing, partitions, and construction purposes.Q: How do I choose between woven steel mesh types for my project?
A: Consider the required strength, corrosion resistance, and mesh size for your application. Stainless steel suits harsh environments, while mild steel is best for general indoor uses.Post time: Jul . 05, 2025 08:02