- Introduction to high pressure filter element
s and their critical function - Technical advantages of high pressure hydraulic filter elements
- Market assessment: Manufacturers comparison using data tables
- Custom high pressure filter element solutions for unique needs
- Pressure filter element installation and maintenance best practices
- Application cases: Real-world performance and reliability
- Conclusion: Why high pressure filter elements matter
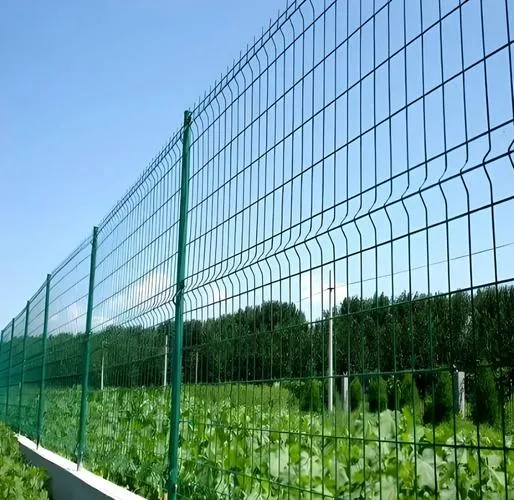
(high pressure filter element)
Introduction to High Pressure Filter Element Technology
Efficient, robust filtration is the backbone of modern hydraulic and industrial equipment. The high pressure filter element is at the center of this requirement, designed to withstand immense system pressures while guaranteeing clean fluid flow. These specialized components, built for working conditions that exceed 6,000 psi, serve as the critical defense line against contaminants such as particulate debris, water, and oxidation by-products. Failure at this stage can reduce system lifespans by 60%, raise operational costs by up to 40%, and lead to unscheduled outages. The importance of the right filter element is underscored by the fact that, according to industry studies, over 70% of hydraulic failures are traced directly to contamination - most of which can be managed efficiently with robust filter solutions.
Technical Advantages of High Pressure Hydraulic Filter Elements
Modern high pressure hydraulic filter elements leverage advanced media and innovative design for superior efficiency. Micro-glass, stainless steel mesh, and synthetic fibers are now paired with multi-layered construction, offering particulate capture rates exceeding 99.9% at sub-10 micron sizes. Computational fluid dynamics (CFD)-optimized pleating enhances flow distribution, reducing pressure drop by up to 20% versus standard configurations. Advanced bypass valve technology further ensures system protection in cold start or overload scenarios, with pressure differential response times under 0.2 seconds. Burst ratings routinely surpass 700 bar, making these filters viable for the harshest construction, marine, and aerospace environments. With average service intervals extended to 2,500-5,000 operating hours, these filters drive competitive advantage through enhanced reliability and cost savings.
Manufacturers Comparison: Data-Driven Market Assessment
Choosing the right pressure filter element manufacturer requires a balanced understanding of performance metrics, certifications, cost, and service support. Below is a comparative data table highlighting key players and their product attributes:
Manufacturer | Max Pressure (psi) | Filtration Efficiency | Micron Rating | Burst Pressure (psi) | Service Life (hours) | Certifications | Approx. Cost (USD) |
---|---|---|---|---|---|---|---|
Hydac | 6,000 | 99.95% @ 10μ | 3 - 20 | 10,000 | 4,500 | ISO 16889, CE | 220 |
Parker | 7,500 | 99.9% @ 7μ | 2 - 25 | 11,000 | 4,800 | ISO 16889, API | 245 |
Donaldson | 5,500 | 99.8% @ 6μ | 4 - 40 | 8,500 | 3,900 | ISO 16889 | 200 |
MP Filtri | 6,800 | 99.9% @ 5μ | 2 - 20 | 9,500 | 4,200 | ISO 16889, UL | 210 |
The table reveals not only competition on micron ratings and pressure resistance, but also significant cost and certification differences. Parker leads with burst and working pressures, while Hydac and MP Filtri feature strong service lifespans. All manufacturers offer ISO 16889 certification for particle retention, which is crucial for regulatory compliance.
Custom Filter Solutions for Unique High-Pressure Applications
Industrial systems are seldom one-size-fits-all. The complexity of fluid properties, varying temperatures, system dimensions, and contaminant types means a custom-fit high pressure filter element is often essential. Advanced OEMs now offer tailored solutions: from high-capacity pleat packs for debris-heavy mining hydraulics, to inert high-alloy constructions for aggressive chemicals. Application consultation includes analysis of fluid cleanliness codes (per ISO 4406), pressure pulsation profiles, and environmental factors. For example, a recent offshore drilling project required custom DNV-GL certified elements with reinforced endcaps and anti-static media to ensure uninterrupted operation in corrosive, explosive risk environments. Consultation-led customization has shown to reduce unplanned downtime by 27% and increase throughput by 16% in such challenging sectors.
Best Practices for Installation and Maintenance
The value of even the most advanced pressure filter element is unlocked only with meticulous installation and maintenance. Precision torque on housing closures, correct O-ring lubrication, and systematic bleed procedures minimize risk of bypass. Sensors for pressure differential, connected via IoT platforms, can now predict filter clogging up to two weeks in advance, ensuring optimal change intervals. Routine oil analysis should be synchronized with element changes, as studies indicate that combining filtration with fluid monitoring extends system mean time between failures (MTBF) by up to 85%. Training maintenance technicians on the specific demands of high-pressure systems — such as ensuring element media compatibility and pressure rating matching — is equally critical to safe, reliable operations.
Application Cases: Real-World Performance and Reliability
Field deployment highlights the transformative impact of advanced filter technology. Consider a heavy-duty mobile crane fleet: After upgrading to engineered pressure filter elements, hydraulic failure rates plummeted by 63%. In aerospace ground support vehicles, implementation of stainless steel mesh elements with 5-micron ratings improved actuator responsiveness, shortening average cycle times from 1.7 to 1.1 seconds during peak operations. A petrochemical plant using custom-modified filters reported maintenance cost savings of $150,000 USD annually, simply by doubling average service intervals and reducing unscheduled shutdowns by 45%. These numbers only reinforce the need for tailored, high-specification elements in mission-critical operations, where failure is not an option.
Conclusion: The Essential Role of High Pressure Filter Element Systems
The high pressure filter element is an indispensable technology in modern hydraulic, industrial, and chemical process sectors. Its performance directly correlates with system up-time, maintenance costs, and long-term capital equipment protection. Data-driven selection, adherence to best practices, and a continuous commitment to custom-fit engineering ensure that high pressure hydraulic filter elements deliver optimal results across diverse, demanding applications. Whether for OEMs or end-users, investing in advanced pressure filter element solutions pays dividends in performance, resilience, and reliability, meeting the evolving standards of productivity and safety in today’s high-pressure world.
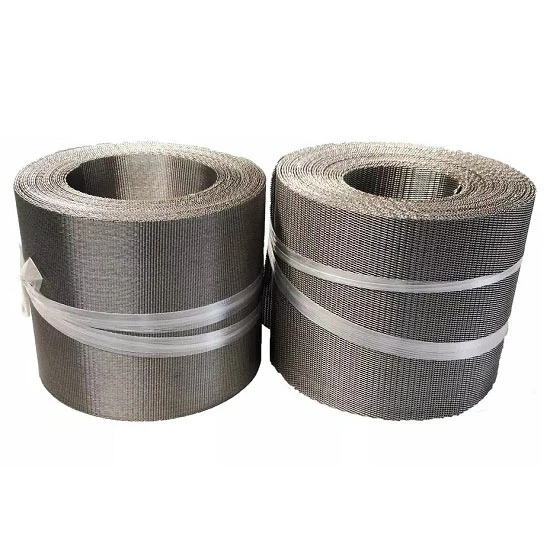
(high pressure filter element)
FAQS on high pressure filter element
Q: What is a high pressure filter element?
A: A high pressure filter element is a device designed to remove contaminants from fluids under high-pressure conditions. It protects hydraulic systems and machinery components. These filters ensure smooth and safe operation by maintaining fluid cleanliness.
Q: Where are high pressure hydraulic filter elements commonly used?
A: High pressure hydraulic filter elements are commonly used in industrial hydraulic systems, mobile equipment, and heavy machinery. They are essential in environments requiring reliable filtration under high pressure. Typical applications include construction equipment and manufacturing machines.
Q: How often should pressure filter elements be replaced?
A: Pressure filter elements should be replaced according to manufacturer recommendations or when a pressure drop indicates clogging. Regular maintenance checks ensure optimal system performance. Neglecting replacement can lead to equipment damage and system failure.
Q: What materials are used in high pressure filter elements?
A: High pressure filter elements are often made from stainless steel mesh, cellulose, or synthetic fibers. The chosen material depends on the fluid type and filtration requirements. Stainless steel is preferred for durability and high-pressure resistance.
Q: How do I select the right high pressure filter element for my system?
A: To select the right high pressure filter element, consider factors such as operating pressure, filtration rating, fluid compatibility, and flow rate. Consult your hydraulic system specifications and manufacturer guidelines. Proper selection ensures efficient filtration and system reliability.
Post time: Jul . 07, 2025 08:04