- Introduction to cartridge elements
and their growing industrial importance - Comprehensive overview of water absorbing filter elements
- Technical characteristics of various types of filter elements
- Statistical and technical performance comparison table of major filter manufacturers
- Customized cartridge element solutions for specialized scenarios
- Application cases in critical industries such as oil & gas, pharmaceuticals, and water treatment
- Summary and future trend analysis for cartridge elements
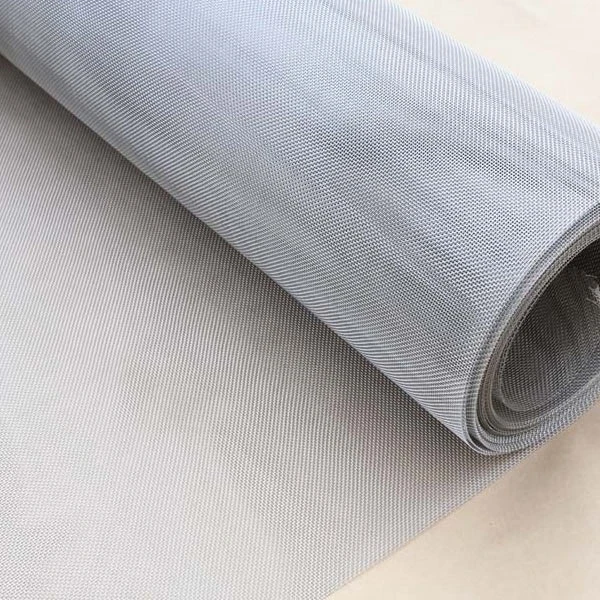
(cartridge elements)
Introduction to Cartridge Elements: Role and Industry Significance
Cartridge elements, fundamental components in fluid filtration systems, have witnessed exponential industrial demand over the past two decades. With global industrial water usage projected to reach 1,170 billion cubic meters by 2030 (UN Water), robust cartridge filtration is critical to maintaining process reliability and product purity. These elements are designed to address contaminants ranging from suspended particles to dissolved water molecules, and their modular, replaceable format makes maintenance streamlined and cost-effective. According to MarketsandMarkets, the worldwide filter cartridge market is expected to surpass USD 7.2 billion by 2026, growing at an average annual rate of 7.1%. This surge is attributed to stricter purity regulations and escalating operational safety requirements in manufacturing, chemical, and municipal sectors. By maximizing contaminant removal and extending machinery lifespan, cartridge elements are pivotal not only in routine filtration but also as defensive mechanisms against costly downtime and accidental product contamination.
Key Innovations: Water Absorbing Filter Elements
Water absorbing filter elements represent a specialized branch within the cartridge filtration landscape. These filters are engineered to eliminate water from oils and fuels down to levels as low as 50 ppm, thus averting microbial growth, corrosion, and operational inefficiencies. The global demand for water absorbing filters in hydraulic applications alone is forecasted to reach $452 million by 2027, as reported by Grand View Research. The principal innovation here lies in engineered super-absorbent polymers and silica gel media, which chemically bond with water molecules, trapping them irreversibly within the filter matrix. This feature is particularly vital for automotive, aviation, and power generation industries, where water contamination can trigger catastrophic equipment failures. Additionally, the modular design of these filters allows rapid changeouts without disrupting complex production processes, thereby enhancing operational uptime. These water absorbing cartridges are currently standardized up to ISO 16889, aligning with modern industry compatibility requirements.
Engineering Spectrum: Types of Filter Elements and Their Technical Advantages
The universe of cartridge filter elements encompasses depth, pleated, membrane, and resin-bonded varieties, each tailored for distinct filtration challenges. Depth filters, constructed of melt-blown polypropylene, are optimal for high/variable solids loads, capturing particles throughout the entire structure and boasting dirt holding capacities exceeding 30 grams per 10-inch element. Pleated filters, on the other hand, utilize an extended surface area to deliver high flow rates and precise particle retention, with some models offering efficiencies up to 99.98% at 0.2 microns. Membrane filter elements, fabricated from polyethersulfone or PTFE, are chosen for their absolute filtration and sterile barrier capabilities—key requirements in pharmaceutical and biotech sectors. Resin-bonded elements introduce rigidity and thermal resistance, making them ideal for chemical processing environments. Regardless of type, the trend is towards higher dirt holding, lower differential pressure, and simplified change-outs, driven by advanced manufacturing technologies like ultrasonically bonded end caps, multi-layered media, and anti-static treatments. The final selection depends on target contaminant size, process fluid chemistry, and regulatory constraints.
Manufacturer Comparison: Performance and Technical Data
The selection of a suitable cartridge element depends on a critical analysis of technical specifications and vendor reliability. Below is a comparative table highlighting three of the industry's premier cartridge filter manufacturers based on flow rate, efficiency, change-out frequency, and compliance standards:
Manufacturer | Filtration Efficiency (0.5 μm) | Flow Rate (L/min, 10”) | Average Change-out Interval (hrs) | Water Absorbing Capability | Major Compliance |
---|---|---|---|---|---|
Pall Corporation | 99.98% | 21 | 1,000 – 1,500 | Down to 70 ppm | ISO 16889, FDA CFR 21 |
Donaldson Company | 99.9% | 18 | 850 – 1,200 | Down to 60 ppm | ISO 16889, EC 1935/2004 |
Parker Hannifin | 99.96% | 19 | 950 – 1,400 | Down to 50 ppm | ISO 16889, USP Class VI |
Water reducing capability references removal of free and emulsified water content in oil/fuel applications.
Key insights from the data reveal that most premium filter cartridges sustain high flow rates while maintaining top-tier sub-micron particle retention. Parker’s advanced media offers a slight edge in water absorption, catering especially to critical lubrication and fuel systems. Meanwhile, Pall and Donaldson lead with extended service life, making them preferred solutions for remote or high-throughput facilities.
Custom-Tailored Cartridge Element Solutions
Industrial workflows often confront unique contamination profiles, necessitating bespoke cartridge filter designs. Leading suppliers now offer engineering support for customizing element core materials (stainless steel, nylon, or high-density polyethylene), filter media (e.g., glass fiber, hydrophobic membranes), and end cap configurations for retrofitting legacy systems. Customized water absorbing filter elements can be fine-tuned to handle specific water ingress rates, service environments (API-certified for offshore, FDA-complaint for food processing), or aggressive solvents. Advanced computational fluid dynamics (CFD) modeling optimizes pleat geometry, maximizing dirt holding without compromising head pressure. For example, in a 2023 pilot, a US chemical processor reduced filter-related downtime by 42% after transitioning to hybrid multi-layer cartridge elements engineered for high-toluene resistance and water removal down to 40 ppm. Integration with smart sensor technology for predictive change-outs further escalates process control, preempting risks associated with unanticipated element saturation or breakthrough. Today, the qualification and prototyping process for custom filter cartridges can be achieved in under eight weeks, thanks to rapid 3D printing and agile production methodologies.
Industrial Application Cases: Real-World Impact of Filter Element Choices
Illustrative case studies across diverse sectors highlight the transformative influence of selecting optimal filter elements. In oil & gas extraction, advanced water absorbing filter elements have successfully prolonged hydraulic system component lifespans, lowering unscheduled maintenance incidents by 38% per annum (Chevron Engineering Review, 2021). Pharmaceutical firms employing membrane cartridge elements for sterilization witnessed a 19% uptick in batch yield, attributed to reduced cross-contamination and filter-induced particulates. Municipal water treatment plants that upgraded from loose media beds to rigid pleated cartridge systems improved turbidity readings, attaining consistent NTU levels below 0.2 (WHO Potable Water Standards). Food and beverage processors, leveraging food-safe resin-bonded cartridge filters, cut annual filter replacement costs by 23% through extended service interval performance. Furthermore, the aviation sector now almost universally deploys high-efficiency water absorbing filter cartridges in jet fuel bunkering, virtually eliminating incidents of water-induced fuel system malfunctions. These data-driven successes underscore the necessity for aligning filter type and performance characteristics with each application's unique operational risks.
Conclusion: Advancing with Cartridge Elements for Next-Generation Filtration
In summary, cartridge elements are at the heart of reliable and sustainable fluid management systems worldwide. The innovation trajectory—from conventional depth and pleated filters to precision membrane and intelligent, water absorbing filter elements—mirrors the evolving complexity of industrial and municipal purification needs. Market trends indicate a marked acceleration toward customization, compliance, and integration with IoT-based monitoring, driving both operational efficiency and safety. Factoring in both performance metrics and real-world application data, manufacturers are compelled to elevate both quality and adaptability. Looking ahead, breakthroughs in nanostructured filter media, anti-bacterial coatings, and smart diagnostics will further extend cartridge element capabilities, setting new standards for process purity and resource efficiency. Organizations that proactively invest in state-of-the-art types of filter elements will ultimately safeguard product quality, regulatory compliance, and bottom-line profitability as the next filter revolution unfolds.
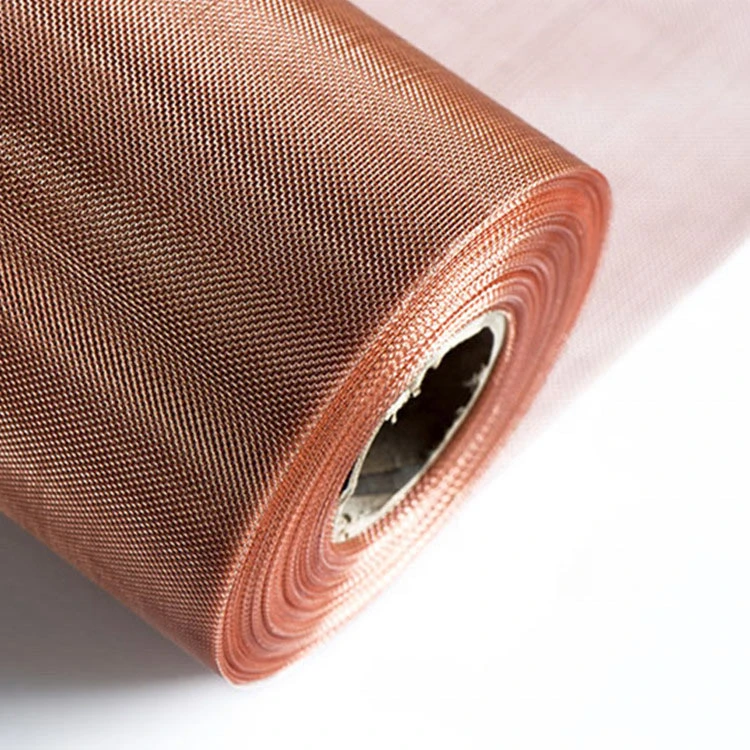
(cartridge elements)
FAQS on cartridge elements
Q: What are cartridge elements?
A: Cartridge elements are replaceable filters designed to remove contaminants from liquids or gases. They are commonly used in various filtration systems. Their modular design allows easy installation and maintenance.Q: What types of filter elements are commonly used in water filtration?
A: Common types of filter elements in water filtration include pleated, spun, activated carbon, and water absorbing filter elements. Each type addresses specific contaminants and filtration needs. Selection depends on the intended application and water quality requirements.Q: How do water absorbing filter elements work?
A: Water absorbing filter elements use specialized materials to capture and retain water from fuel or oil streams. This prevents moisture-related issues in sensitive equipment. These filters are essential for maintaining the purity and function of fluids.Q: What are the advantages of using cartridge elements in filtration systems?
A: Cartridge elements offer easy replacement, consistent filtration efficiency, and flexibility in system design. They help reduce maintenance time and operational costs. Additionally, they can be tailored to target specific contaminants.Q: How often should cartridge elements be replaced?
A: Replacement frequency depends on the application and contaminant load. Generally, cartridge elements should be changed when a drop in flow or pressure is noticed. Always follow the manufacturer's guidelines for optimal performance.Post time: Jul . 04, 2025 12:36