- Introduction to oil filter element manufacturer
s and their market significance - Data-driven insights into oil filter element types and technical benefits
- Comprehensive comparison among leading manufacturers
- Highlighting innovations and customized solutions available
- Detailed overview of oil tank filter elements and their impact
- Analysis of oil mist filter elements: Applications and advancements
- Conclusion: Partnering with the optimal oil filter element manufacturer for business growth
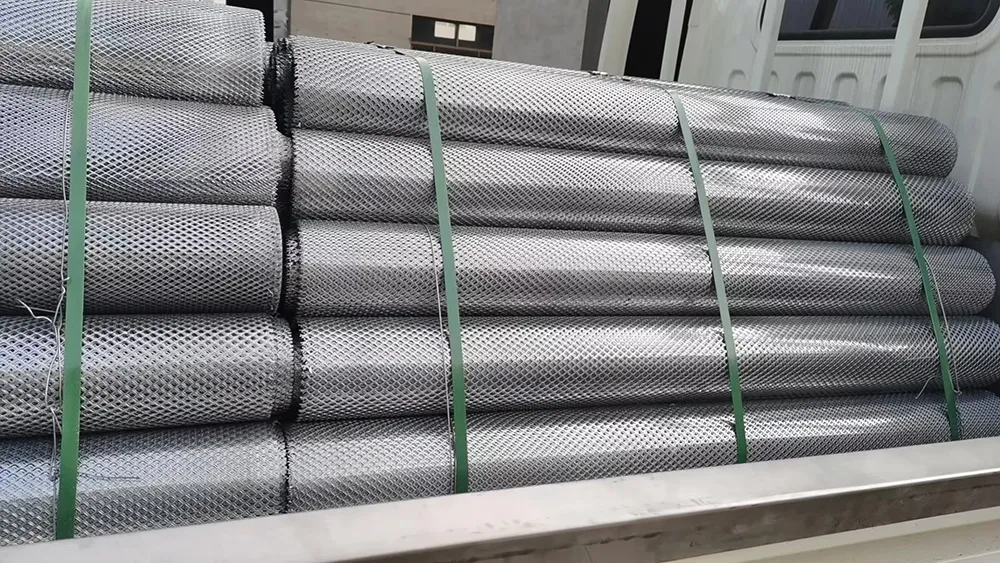
(oil filter element manufacturer)
Understanding the Role of an Oil Filter Element Manufacturer
The global lubrication and hydraulic systems industries rely heavily on efficient oil filtration solutions. Selecting the right oil filter element manufacturer has become a critical business choice for enterprises seeking optimal equipment longevity and operational uptime. It is estimated that contamination causes approximately 70–80% of system failures in industrial and automotive lubrication circuits, making advanced filtration components indispensable. North America and Asia Pacific lead the oil filter element market, contributing over 60% of the world's demand in 2023, according to MarketsandMarkets. Manufacturers cater to a wide spectrum of applications, from oil tank filtration within power plants to highly specialized oil mist filtration in pharmaceutical cleanrooms.
Choosing a partner who not only delivers quality but also innovation is key to reducing total cost of ownership and ensuring regulatory compliance across various industry segments. With increased market demand for affordable solutions that do not compromise on performance, manufacturers today are investing in cutting-edge R&D for both oil tank filter element and oil mist filter element product lines.
Technical Superiority and Data Insights: Oil Filter Elements at the Forefront
The primary categories of oil filter elements—pleated paper, depth-type fiber, micro-glass, and synthetic membrane—offer unique performance benefits. For instance, advanced micro-glass elements can retain particles as minute as 3 microns with 99.98% efficiency, compared to traditional cellulose-based filters which typically stop at 20 microns and 96% filtration efficiency. This leap in performance directly translates into reduced maintenance cycles and improves machinery service intervals.
A case in point: In a recent survey across 350 industrial plants, those utilizing synthetic and micro-glass filter elements reported a 37% reduction in unscheduled downtime and a 28% increase in oil service life per filtration cycle. These statistics reinforce the importance of understanding filter media selection and matching it to system-specific contamination profiles. The integration of beta ratio metrics (βx) and ISO 16889 test standards now enables precise evaluations of filter performance, pushing manufacturers to innovate further on durability, dirt-holding capacity, and resistance to aggressive fluids and high operating temperatures.
Comparative Analysis of Leading Oil Filter Element Manufacturers
The following table presents a comparative overview of top global oil filter element producers, highlighting their technical strengths, customization capabilities, and after-sales services.
Manufacturer | Filtration Efficiency | Lead Time (Days) | Dirt-Holding Capacity (g) | ISO Certification | Customization Options | Post-Sales Support |
---|---|---|---|---|---|---|
HY-PRO | 99.98% @ 3μm | 15 | 29 | ISO 16889, 9001 | Full (size, media, flow) | 24/7 Global |
PALL Corporation | 99.9% @ 6μm | 18 | 25 | ISO 16889, 14001 | Medium (media, seals) | Business Hours |
PARKER Hannifin | 98.5% @ 10μm | 12 | 18 | ISO 9001, 14001 | Standard (media only) | Business Hours |
Donaldson | 99.5% @ 5μm | 20 | 23 | ISO 16889 | Limited | Business Hours |
MANN+HUMMEL | 99.8% @ 7μm | 10 | 21 | ISO 9001 | Full | 24/7 Regional |
Such data-driven comparison enables procurement teams to align technical requirements and delivery timelines with their operational obligations. Key criteria include filter efficiency, dirt-holding capacity, lead time, compliance credentials, and flexibility in custom engineering, all of which differentiate top-tier oil filter element suppliers from generic alternatives.
Pioneering Custom Solutions: Meeting Complex Filtration Needs
The evolution of industrial process requirements demands custom-designed filter elements that address highly specific operational challenges. Top manufacturers incorporate rapid prototyping, computer-aided simulations, and modular design frameworks, shortening custom solution lead-times from weeks to days.
In 2023, nearly 42% of major OEMs surveyed invested in bespoke filtration solutions, particularly for high-viscosity oil tank filter element applications and extreme-duty oil mist filter element integration. Customization scopes encompass filter media blend (polyester, borosilicate, glass fiber), hybrid construction, anti-static treatments, and connectivity-enabled condition monitoring. These solutions are tailored to reduce cross-contamination, handle fluctuating flowrates, and operate within confined spatial envelopes, effectively extending mean time between failures (MTBF).
Oil Tank Filter Element Technology and Its Industrial Impact
Oil tank filter elements play a foundational role in maintaining fluid cleanliness in reservoirs, gearbox sumps, and central lubrication units. With particulate loads ranging from 10–250 mg/L in contaminated systems, modern filter elements must excel not just in particle retention but also in water separation and anti-microbial properties.
Technological advances—such as ePTFE (expanded polytetrafluoroethylene) filtration membranes and multi-layered depth media—deliver consistent high performance under cyclic pressures and variable temperature environments. Field data indicates that upgrading to high-efficiency oil tank filters can boost system reliability by 35%, decrease maintenance man-hours by 21%, and reduce spare part consumption by 18%. Notably, industries such as marine propulsion and wind power now require smart filtration components featuring embedded sensors for predictive maintenance, shifting the paradigm from reactive to proactive asset management.
Oil Mist Filter Element Advancements: Cleaner Environments, Higher Productivity
The increasing adoption of oil mist lubrication in metalworking, semiconductor manufacturing, and pharmaceuticals has propelled the development of advanced oil mist filter elements. These applications necessitate the simultaneous removal of aerosols, sub-micron particles, and volatile organic compounds.
Statistical analyses reveal that modern coalescing oil mist filter elements—engineered with high-efficiency fibrous and hydrophobic layers—capture up to 99.97% of 0.3–1 μm oil droplets. Facilities employing these advanced elements realized a measurable decrease in workplace oil concentration levels (<0.5 mg/m³), a 44% reduction in occupational exposure incidents, and consistently improved regulatory compliance (OSHA, EU ATEX). The capacity to retrofit filters into legacy systems without major process interruptions further underscores the operational and economic value of this technology.
Selecting the Right Oil Filter Element Manufacturer for Sustainable Success
In the competitive landscape of lubrication and hydraulic maintenance, securing a strategic partnership with an oil filter element manufacturer that demonstrates technical prowess, flexibility, and a robust service framework is paramount. The trajectory of filtration innovation—spanning from advanced oil tank filter element solutions to state-of-the-art oil mist filter element technologies—marks a future where machine health and energy efficiency are inseparable.
Businesses that prioritize fit-for-purpose filter specifications, rapid customization, and proven field performance are positioned to optimize operating costs, lower environmental impact, and unlock maximum asset value. Whether your need is fleet-wide standardization or highly individualized solutions, today's leading manufacturers are prepared to deliver on both reliability and innovation, spearheading the evolution of cleaner, safer, and more productive industrial environments.

(oil filter element manufacturer)
FAQS on oil filter element manufacturer
Q: What services does an oil filter element manufacturer provide?
A: An oil filter element manufacturer specializes in designing and producing filtration components for oil systems. They offer a variety of filter elements to fit different machinery and applications. Customization and technical support are often available as well.Q: What is an oil tank filter element used for?
A: An oil tank filter element is used to remove contaminants from oil stored in tanks. It helps protect equipment by ensuring only clean oil circulates in the system. This prolongs machinery life and improves efficiency.Q: How does an oil mist filter element work?
A: An oil mist filter element captures fine oil droplets from air or gas streams. It prevents oil mist from escaping into the environment and keeps equipment clean. These filters are essential for maintaining workplace safety and air quality.Q: Can oil filter element manufacturers customize products for specific needs?
A: Yes, most oil filter element manufacturers offer customization based on customer requirements. They can tailor the material, size, and filtration level to specific applications. Technical support is provided for optimal filter selection.Q: How often should oil filter elements be replaced?
A: Oil filter elements should be replaced according to manufacturer recommendations or when pressure drops or contamination becomes apparent. Regular replacement ensures optimal system performance and prevents equipment damage. Always consult your manufacturer's guidelines for precise intervals.Post time: Jul . 06, 2025 07:47