- Market impact of welded wire mesh in construction and agriculture
- Technical advantages over traditional fencing methods
- Comparative analysis of leading welded wire mesh manufacturers
- Customization capabilities for specialized applications
- Material selection and engineering specifications
- Industry-specific application case studies
- Future innovations in wire mesh fabrication
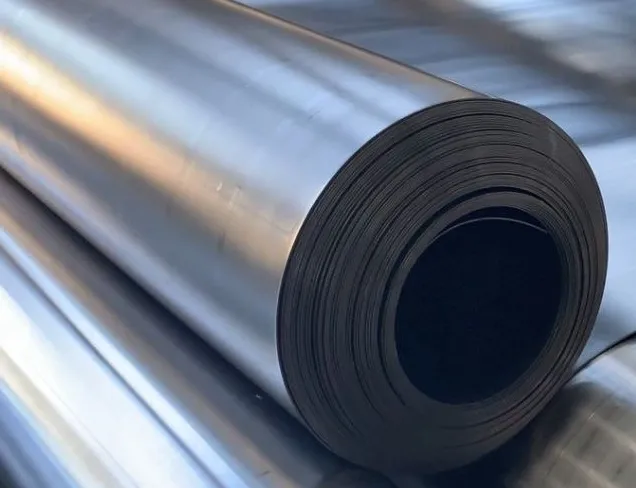
(welded wire mesh manufacturers)
Driving Global Infrastructure Through Welded Wire Mesh Manufacturers
Welded wire mesh has transformed structural reinforcement across multiple sectors, with the global market projected to reach $15.3 billion by 2028, growing at 6.2% CAGR according to Industry Research Group data. These manufacturers enable modern construction through standardized panels that accelerate project timelines by up to 40% versus hand-tied alternatives. The manufacturing process begins with high-tensile steel wire drawn to diameters ranging from 2mm to 12mm, then precision-welded using automated resistance welders operating at 7-15 panels per minute. Quality assurance protocols demand testing every 10th panel for weld shear strength and dimensional tolerances under ISO 9001:2015 certification standards.
Engineering Advantages of Modern Wire Mesh Systems
Galvanized welded mesh outperforms traditional construction methods with measurable advantages. The electro-galvanizing process provides 85µm zinc coatings that withstand salt spray testing for over 1,200 hours. Structural testing reveals:
- Load distribution capacity increased by 60% compared to chain-link fencing
- Installation labor costs reduced by 50-75% through prefabricated panels
- Service life exceeding 25 years in corrosive coastal environments
Hot-dip galvanized variants offer superior protection with zinc coatings exceeding 250µm thickness. Manufacturers now incorporate accelerated corrosion testing into quality control, simulating 20-year exposure in 90-day laboratory conditions to validate performance claims.
Top Welded Wire Mesh Manufacturers Comparison
Manufacturer | Specialization | Production Capacity (monthly) | Certifications | Delivery Lead Time |
---|---|---|---|---|
StructuraMesh Inc. | Heavy-duty construction grids | 12,500 tonnes | ISO 9001, CE, ASTM A185 | 2-3 weeks |
SecureBound Fencing | Perimeter security systems | 7,800 tonnes | ISO 1461, DIA 18053 | 3-5 weeks |
GalvSteel Industries | Marine-grade GI mesh | 9,200 tonnes | ASTM A641, AS 4687 | 4-6 weeks |
Supply chain benchmarks show leading manufacturers maintain rolling inventory for standard aperture sizes (100x100mm to 50x50mm) while achieving 99.1% on-time delivery rates. The most advanced facilities operate continuous galvanizing lines processing 12 tonnes/hour with automated optical inspection systems.
Custom Fabrication Capabilities
Specialized applications drive innovation in fabrication techniques. For seismic reinforcement, manufacturers create mesh with variable wire gauges that transition from 6mm at grid intersections to 10mm at load points. Highway barrier systems now incorporate:
- Ultra-high mesh densities (50mm x 25mm apertures)
- Double-wire welding at critical junctions
- Custom curvature bending for retaining walls
Advanced producers utilize robotic bending cells achieving ±0.5mm tolerance on curved sections. Recent innovations include zinc-aluminum-magnesium coatings that extend maintenance intervals by 4x compared to standard GI coatings.
Material Selection Criteria
Manufacturing specifications directly impact performance in demanding environments. Cold-drawn wire with tensile strength of 550-750 N/mm² provides flexibility without sacrificing durability. When selecting materials:
- Marine installations require 300 g/m² zinc coatings
- Agricultural applications use PVC encapsulation over galvanizing
- High-temperature zones mandate stainless steel wire alloys
Leading welded wire fence manufacturers now deploy multi-layer corrosion protection systems that combine hot-dip galvanizing with proprietary organic sealants. Third-party validation confirms these systems retain 95% structural integrity after 15 years in Class IV corrosion zones.
Industrial Application Case Studies
The versatility of welded mesh manifests in these installations:
- Transportation: 83km highway project with customized 4.5m barrier panels reduced installation time by 60% using prefabricated sections
- Agriculture: Poultry farms increased structural spans by 40% while decreasing material costs through optimized wire gauges
- Energy: Offshore platforms utilized nickel-alloy meshes that withstood 25-year salt exposure without degradation
Commercial developments now incorporate architectural mesh façades featuring powder-coated finishes in custom RAL colors while maintaining structural load ratings. Post-installation studies show maintenance costs reduced by 35% compared to traditional reinforcement methods.
GI Welded Mesh Manufacturers Forging Industry Futures
Manufacturing innovation continues to accelerate with laser-welded mesh entering niche markets, achieving 0.1mm precision tolerances. The most advanced welded wire mesh manufacturers now implement Industry 4.0 practices with:
- AI-powered quality control systems detecting micro-fissures
- Automated inventory management reducing lead times to 72 hours
- Environmental compliance protocols cutting carbon emissions by 40%
Research partnerships with material science institutions have produced graphene-enhanced zinc coatings demonstrating 3x standard corrosion resistance. As modular construction gains prominence, welded mesh manufacturers are positioned to enable rapid deployment of infrastructure that meets increasingly stringent global standards.
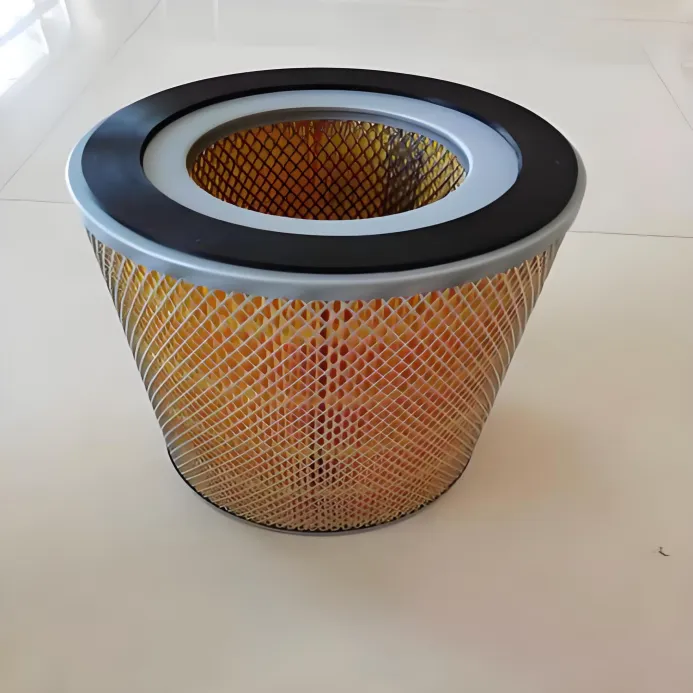
(welded wire mesh manufacturers)
FAQS on welded wire mesh manufacturers
Q: What are common applications of welded wire mesh from manufacturers?
A: Welded wire mesh is widely used in construction for concrete reinforcement, fencing, and industrial security screens. Manufacturers produce varied sizes for diverse projects like residential and agricultural settings. Their products ensure durability and long-term performance.
Q: Why choose specialized welded wire fence manufacturers for perimeter security?
A: These manufacturers focus on creating robust, tamper-resistant fences ideal for homes, farms, and commercial sites. Their expertise includes using high-tensile wires for enhanced strength and longevity. This specialization guarantees reliable installation and tailored safety solutions.
Q: What benefits do gi welded mesh manufacturers offer compared to standard options?
A: GI welded mesh manufacturers provide galvanized products that resist corrosion and rust, making them perfect for harsh environments like coastal areas. They offer longer-lasting mesh with superior weather resistance. Custom sizes and coatings are available for specific industrial needs.
Q: How do welded wire mesh manufacturers handle customization requests?
A: Manufacturers allow customization of wire gauge, mesh size, panel dimensions, and coatings such as galvanization. They work with materials like stainless steel for unique applications. Quick prototyping and tailored designs help meet project-specific requirements efficiently.
Q: What factors indicate a reliable welded wire fence manufacturer?
A: Look for certifications like ISO, years of industry experience, and positive customer reviews to ensure reliability. Reputable manufacturers use high-quality materials and offer responsive support. They prioritize on-time delivery and thorough quality checks for consistent excellence.
Post time: Jun . 07, 2025 13:02