- Technical advantages of stainless steel wire mesh screens
- Industry comparison of leading manufacturers
- Available customization options
- Key specifications and sizing metrics
- Industry-specific applications
- Installation and maintenance procedures
- Value analysis for industrial buyers
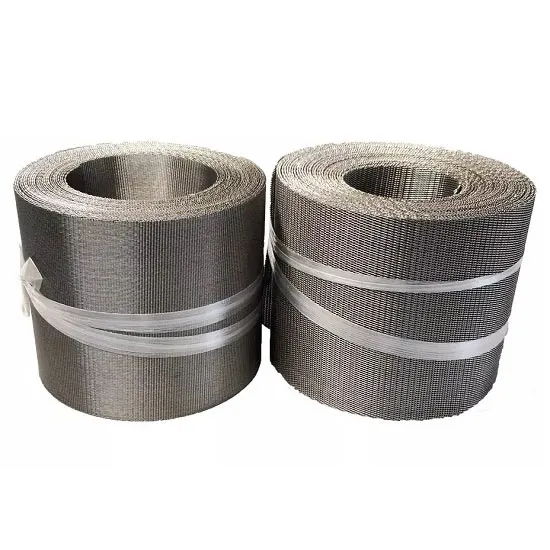
(stainless wire mesh screen)
Understanding Stainless Steel Wire Mesh Screen Applications
Stainless steel wire mesh screens deliver exceptional performance across numerous sectors due to their material resilience. Industrial filtration accounts for 42% of global demand, while architectural applications represent the fastest growing segment with 18% annual growth. These panels resist corrosion even in harsh environments with chlorine concentration levels up to 5,000ppm and temperatures exceeding 600°C (1,112°F). Common manufacturing specifications include ISO 4783-1 for dimensional standards and ASTM E2016 for performance validation.
Material Specifications and Engineering Benefits
Engineers specify stainless wire mesh primarily for its mechanical properties. Grade 316 variants exhibit yield strengths of 215MPa and ultimate tensile strength of 485MPa, far exceeding polymer alternatives. Wire diameters typically range from 0.038mm to 2.50mm, with mesh openings spanning 15 microns to 100mm. Performance data indicates a minimum service life of 10-15 years under standard conditions, with 32% reduction in maintenance costs compared to galvanized alternatives.
Manufacturer Product Comparison
Brand | Materials Offered | Mesh Opening Tolerance | Max Panel Dimensions | Certifications |
---|---|---|---|---|
Company A | 304/316/430 | ±3μm | 2.5m x 6m | ISO 9001 |
Company B | 304/316 | ±5μm | 2m x 4m | AS9100 |
Company C | 304/316/321 | ±2μm | 3m x 12m | ISO 9001, 14001 |
Customization Parameters for Specialized Needs
Custom fabrication options include edge preparation methods ranging from hemmed borders to reinforced frames with precision welding. Mesh configurations support weave densities from 30 to 635 mesh count per linear inch. Suppliers offer panel geometry customization with laser-cutting accuracy within 0.15mm tolerance, capable of producing complex contours for architectural features or specialized machinery. Post-processing treatments include electropolishing for sanitary applications and powder coating in RAL color standards.
Industry-Specific Deployment Models
Chemical processing plants utilize 100-micron opening screens in precipitation tanks, reducing catalyst loss by 27%. In food production, wedge wire filter designs achieve flow rates of 18,000 liters per square meter hourly while meeting 3-A sanitary standards. Architectural applications have incorporated expanded mesh facades in projects requiring up to 80% light transmission with 53% solar heat gain reduction. Mining operations report operational cost reductions of 22% after implementing reinforced wire cloth in trommel screens.
Installation Protocol and Maintenance Management
Proper installation requires tensioning systems maintaining 18-25 N/mm² stress loads for optimal stability. Retaining methods include bolted channels for structural integrity or compression fittings allowing for thermal expansion coefficients of 17 μm/m·K. Maintenance programs incorporate ultrasonic cleaning cycles at frequencies exceeding 35kHz, preserving aperture integrity without abrasion damage. Inspection protocols recommend biannual checks for metal fatigue and deflection tolerances above 1.5mm per meter.
Selecting Premium Stainless Steel Wire Mesh Screen
Industrial buyers should evaluate lifecycle cost analysis rather than initial pricing, as premium grades demonstrate ROI within 14-28 months. For water treatment applications, consider screens with double crimp reinforcement enhancing stability by 39% under hydraulic pressure. Verify material traceability certificates confirming elemental composition meets UNS S31600 standards with low-carbon variants (0.03% max) essential for welding applications. Performance testing documentation should include salt spray results exceeding 1,000 hours in 5% NaCl solution without corrosion formation.
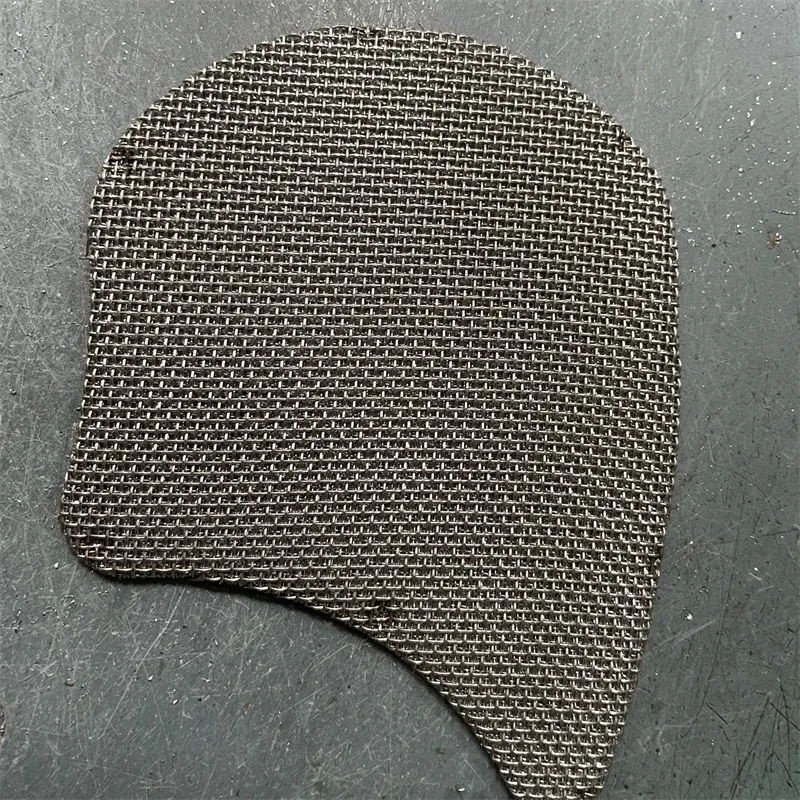
(stainless wire mesh screen)
FAQS on stainless wire mesh screen
以下是围绕核心关键词创建的5组HTML格式FAQ问答:What are the standard stainless steel wire mesh screen sizes?
Q: What are the standard stainless steel wire mesh screen sizes?A: Standard sizes range from 0.001" to 0.063" wire diameters, with mesh counts from 2 to 635 openings per inch. Refer to our stainless steel wire mesh screen sizes chart for precise measurements. Mesh openings vary from 0.0021" to 3.0" depending on the specification.
Why choose stainless steel for wire mesh screens?
Q: Why choose stainless steel for wire mesh screens?A: Stainless steel wire mesh screen offers superior corrosion resistance and durability. It withstands extreme temperatures and harsh environments better than other metals. These properties ensure long-term performance with minimal maintenance.
How is wire mesh screen stainless steel measured?
Q: How is wire mesh screen stainless steel measured?A: Measurements include mesh count (openings per linear inch), wire diameter, and aperture size. Key metrics are listed in our stainless wire mesh specs chart, covering micron retention and open area percentage. Standard industrial tools like calipers verify compliance.
What applications suit stainless steel wire mesh screens?
Q: What applications suit stainless steel wire mesh screens?A: Ideal for filtration, sieving, and separation in food processing, mining, and architecture. Widely used as safety guards, insect screens, and conveyor belts. The material's hygienic properties make it perfect for pharmaceutical and medical uses.
Can stainless wire mesh screens be customized?
Q: Can stainless wire mesh screens be customized?A: Yes, we offer custom wire mesh screen stainless steel in unique sizes, weaves, and alloys. Modifications include edge preparation, panel cutting, and welded reinforcements. Submit your requirements through our technical drawing portal for quotes.
Post time: Jun . 08, 2025 22:16