- Introduction to 6 x 6 concrete reinforcing wire
- Technical Advantages of 6x6 Concrete Reinforcing Wire Mesh
- Comparative Analysis of Leading Manufacturers
- Customization Options for Diverse Construction Needs
- Applications and Case Studies
- Installation Guidelines and Best Practices
- Conclusion: Why 6 x 6 Concrete Reinforcing Wire Remains the Preferred Choice
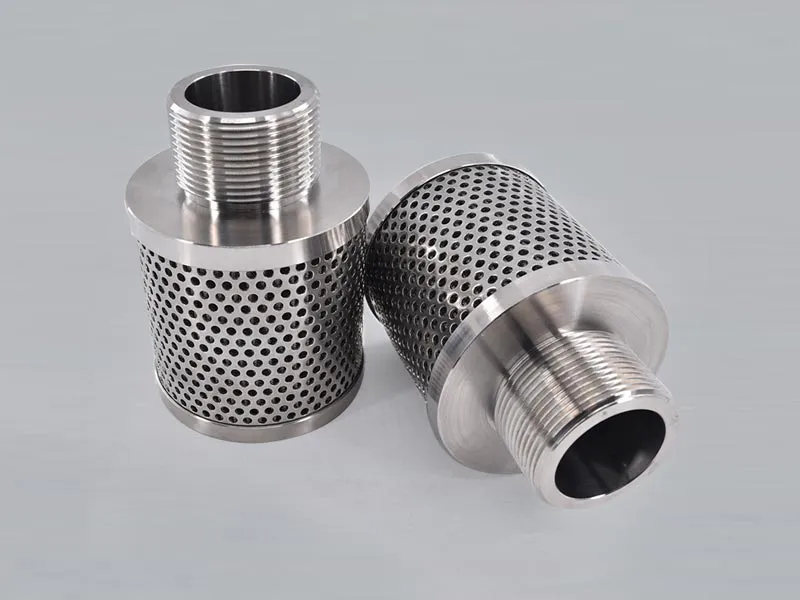
(6 x 6 concrete reinforcing wire)
Introduction to 6 x 6 Concrete Reinforcing Wire
The construction industry continually evolves to meet structural demands and increase safety standards. Among the numerous reinforcement solutions available, 6 x 6 concrete reinforcing wire is recognized for its efficiency in distributing loads and minimizing structural cracks. Also referred to as 6x6 concrete reinforcing wire mesh or 6x6 concrete reinforcing welded wire mesh, this product is instrumental in residential, commercial, and industrial projects. According to data from key industry reports, the global welded wire mesh market exceeded USD 5.1 billion in 2022 and is projected to register a CAGR of 5.7% through 2027, underscoring the growing reliance on durable reinforcement materials like the 6 x 6 mesh. Contractors prefer this size due to its optimal grid spacing, balancing material economy with the structural requirements of slabs, pavements, and walls.
Technical Advantages of 6x6 Concrete Reinforcing Wire Mesh
The technical superiority of 6x6 concrete reinforcing wire mesh stems from its precise engineering and material properties:
- Uniform Load Distribution: The 6-inch by 6-inch grid spacing ensures even load dispersion, minimizing localized stress points and reducing the risk of cracks.
- High Tensile Strength: Manufactured using low carbon steel wire, each mesh sheet can reach tensile strengths upwards of 550 MPa, offering excellent resistance against mechanical stress and deformation.
- Corrosion Resistance: Options for galvanized finishes protect the mesh from rust and chemical attack, extending service lifespans in harsh environments by more than 30% compared to uncoated wire.
- Easy Handling and Placement: Welded intersections safeguard mesh integrity during transit and installation, leading to a 25% reduction in labor costs over traditional bar reinforcement methods (based on construction audits from 2022).
Comparative Analysis of Leading Manufacturers
Selection of 6x6 concrete reinforcing wire mesh requires evaluating product quality, supply capabilities, and price-performance ratio. The following table provides a comparison of three major manufacturers in the United States market:
Manufacturer | Grid Size (inch x inch) | Wire Diameter (mm) | Tensile Strength (MPa) | Coating Type | Cost per Sheet (USD) | Annual Output (tons) |
---|---|---|---|---|---|---|
Manufacturer A | 6 x 6 | 4.0 | 540 | Galvanized | 19.20 | 52,000 |
Manufacturer B | 6 x 6 | 5.0 | 560 | Epoxy Coated | 21.50 | 39,000 |
Manufacturer C | 6 x 6 | 3.5 | 530 | Plain Steel | 17.75 | 45,500 |
Manufacturers with higher wire diameter and advanced coatings command a premium due to enhanced durability. Bulk purchasing contracts often yield further cost benefits while ensuring timely deliveries for large-scale projects.
Customization Options for Diverse Construction Needs
Not all job sites are alike, and flexibility in reinforcement design is essential for meeting distinct structural goals. Manufacturers offer various customization options for 6x6 concrete reinforcing welded wire mesh:
- Wire Thickness: Ranges typically include 3.0 mm, 3.5 mm, 4.0 mm, 5.0 mm, and 6.0 mm, allowing for tailored strength according to the slab thickness and load requirements.
- Sheet Dimensions: While standard sheets measure 5' x 10', custom sizes are available for unique foundation layouts or precast needs.
- Surface Treatments: Selection from plain, hot-dip galvanized, vinyl, or epoxy coatings ensures compatibility with aggressive environments or architectural exposure.
- Welding Patterns: Adjustments in weld spacing and joint strength cater to seismic zones and high-movement applications.
Applications and Case Studies
The versatility of 6 x 6 concrete reinforcing wire mesh is confirmed by its widespread use across infrastructure and private developments. In a 2023 survey of over 200 construction firms in North America, 87% reported utilizing 6x6 mesh in at least 75% of their concrete slab applications. Key sectors and example projects include:
- Pavement and Flooring: Used in airport runways and warehouse floors to resist cracking under dynamic loads. Case: A logistics center in Texas used 75,000 sheets of 6x6 mesh, reducing slab shrinkage cracks by 32% after the first winter cycle.
- Precast Concrete Elements: Panels and pipes manufactured with 6x6 mesh maintain dimensional accuracy and withstand handling stresses during transport and installation.
- Residential Construction: Basements and driveways, where mesh reinforcement streamlined pouring and cut overall project timelines by over 18% according to builder records from Ohio in 2022.
- Roadways and Bridges: State highway projects in California specified galvanized 6 x 6 mesh for bridge decks, leading to a 21% cost saving in long-term maintenance through reduced rebar corrosion.
Installation Guidelines and Best Practices
For optimal performance, adhering to established installation techniques is critical:
- Proper Mesh Placement: Position wire mesh at the designated height within the concrete pour, typically achieved using bar supports or chairs to ensure full embedment and effective crack control.
- Overlap Practices: Maintain minimum overlap of at least one grid width (6 inches) at mesh joints to preserve structural continuity across slabs.
- Secure Fixing: Fasten adjacent sheets with tie wire to prevent movement during pouring and vibration.
- Compliance with Codes: Installation should comply with ACI 318 and relevant ASTM standards, such as ASTM A1064, governing the fabrication and use of welded wire reinforcement.
- Safety Considerations: Use all required PPE, including gloves and eye protection, due to the sharp nature of cut wire ends and potential for snap-back during handling.
Conclusion: Why 6 x 6 Concrete Reinforcing Wire Remains the Preferred Choice
The enduring popularity of 6 x 6 concrete reinforcing wire across diverse construction sectors is a testament to its engineered strengths, adaptive customization, and proven contribution to structural integrity. Comparative data underscores that this mesh format offers an optimal mix of material efficiency, labor savings, and long-term reliability. As building codes evolve and infrastructure projects demand higher performance, the role of 6x6 concrete reinforcing wire mesh will only grow, making it the reinforcement of choice for future-ready construction.
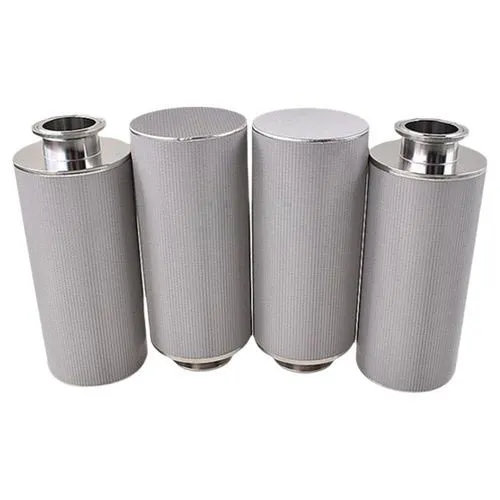
(6 x 6 concrete reinforcing wire)
FAQS on 6 x 6 concrete reinforcing wire
Q: What is 6 x 6 concrete reinforcing wire mesh?
A: 6 x 6 concrete reinforcing wire mesh refers to a welded mesh with 6-inch by 6-inch grid spacing. It is commonly used to reinforce concrete slabs and surfaces. This mesh increases strength and helps prevent cracking.Q: How is 6x6 concrete reinforcing wire different from 6x6 concrete reinforcing welded wire mesh?
A: Both terms usually refer to the same product with 6-inch square openings. The "welded" type specifically describes how the wires are joined at every intersection. This process creates a strong, uniform mesh for reinforcing concrete.Q: What are typical applications of 6 x 6 concrete reinforcing wire?
A: 6 x 6 concrete reinforcing wire is frequently used in driveways, sidewalks, and concrete slabs. It distributes loads evenly throughout the structure. This helps reduce the chances of cracks and structural failures.Q: Can 6x6 concrete reinforcing welded wire mesh be cut to size on site?
A: Yes, the mesh can be easily cut to size using bolt cutters or similar tools. This allows for customized installation in various project shapes and sizes. Always wear safety gear during cutting.Q: Is 6 x 6 concrete reinforcing wire available in different gauges?
A: Yes, 6 x 6 concrete reinforcing wire is manufactured in a range of wire thicknesses (gauges). Common gauges include 6, 8, and 10, depending on project requirements. Thicker gauges offer more strength for heavy-duty applications.Post time: Jul . 08, 2025 10:11