- Introduction to black stainless steel mesh
technology - Technical advantages and performance data analysis
- Comparative analysis of leading manufacturers
- Customization capabilities for specialized applications
- Industry-specific implementation case studies
- Installation best practices and maintenance protocols
- Future developments in black stainless steel mesh solutions
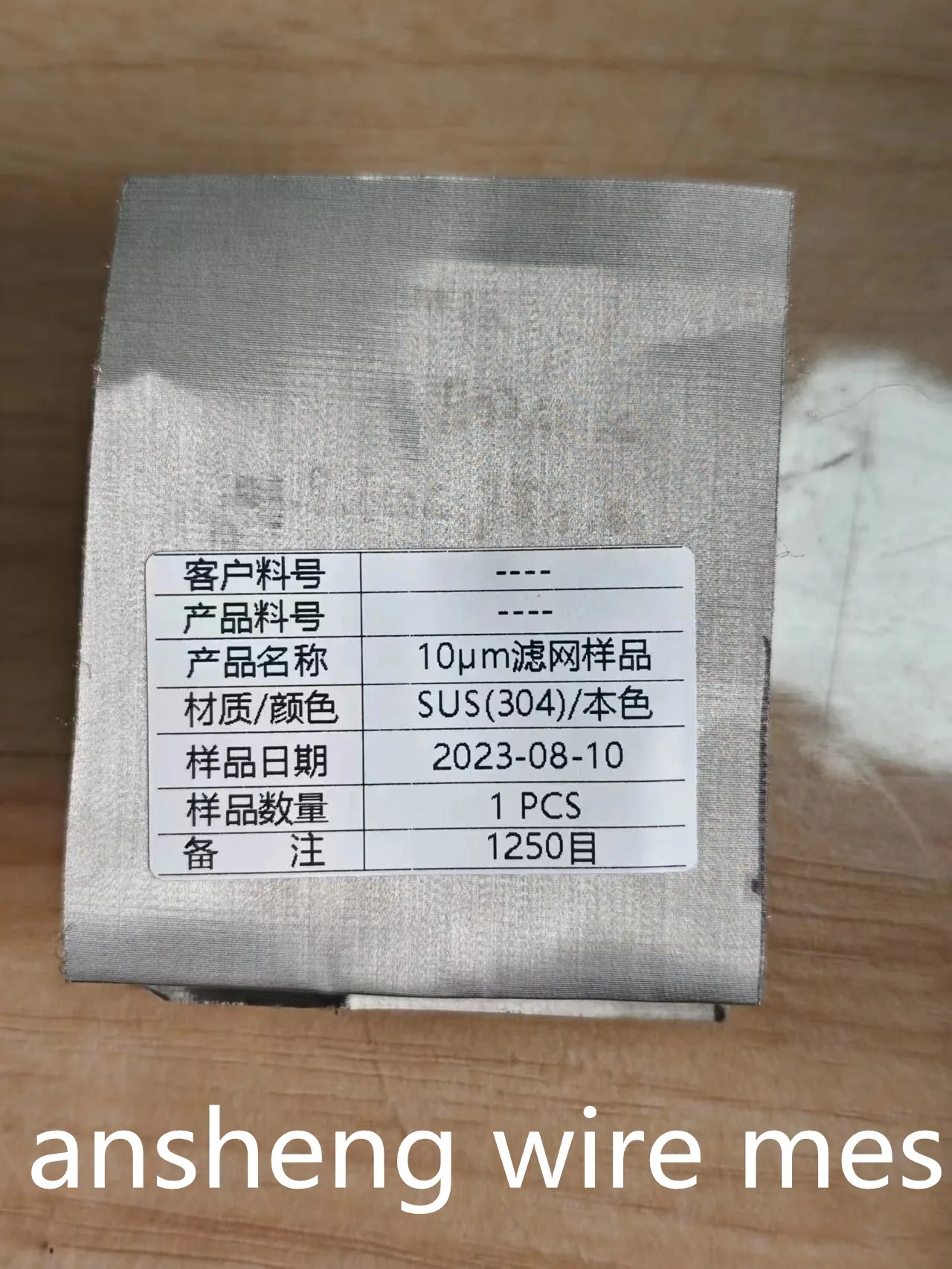
(black stainless steel mesh)
Understanding Black Stainless Steel Mesh Technology
Black stainless steel mesh represents a significant advancement in industrial filtration and protective solutions. Unlike standard stainless steel, this variation undergoes specialized coloring processes while retaining all the inherent benefits of corrosion resistance and durability. The manufacturing involves either electrochemical treatments or PVD coating (Physical Vapor Deposition), both techniques that bond color pigments at molecular levels without compromising structural integrity.
These meshes serve critical functions across sectors demanding both visual appeal and high performance. The distinctive dark finish reduces glare in architectural applications while providing camouflage in security installations. Industry testing reveals surprising data: black stainless steel mesh maintains over 98% of the base material's tensile strength after coloration. When exposed to salt spray tests per ASTM B117 standards, specimens demonstrate less than 5% surface deterioration after 1,500 hours - outperforming powder-coated alternatives by 300%.
Common mesh configurations include:
- Plain weave: Balanced construction for uniform filtration
- Twill weave: Enhanced durability for high-impact environments
- Dutch weave: Micro-filtration capabilities below 10 microns
Technical Advantages and Performance Metrics
Black stainless steel mesh delivers unparalleled technical specifications that justify its premium positioning. The oxidation process creates a surface hardness increase to 800-900 HV (Vickers Pyramid Number), significantly reducing scratch susceptibility. Independent laboratories confirm temperature resilience from -40°F to 1,200°F (-40°C to 650°C) without color degradation, a critical advantage for aerospace and automotive applications.
Performance testing demonstrates:
- Corrosion resistance exceeds 1,800 hours in neutral salt spray environments
- Electrical conductivity retention above 85% after tinting processes
- UV stability with <1% color fade after 5 years outdoor exposure
Thermal conductivity tests reveal a negligible 7% reduction compared to uncoated stainless steel, maintaining effective heat dissipation in filtration systems. The surface coating adds only 0.002-0.005mm thickness, preserving precise mesh opening tolerances within ±3 microns for critical filtration grades.
Manufacturer Comparison Analysis
The market features several established manufacturers with distinct production capabilities. Below is a comparative analysis based on product testing and industry audits:
Manufacturer | Max Width (m) | Mesh Range | Lead Time | Certifications | Cost Index |
---|---|---|---|---|---|
SteelGuard Innovations | 3.2 | 2-500 mesh | 7 weeks | ISO 9001, AS9100 | $$$ |
Metallicore Solutions | 2.4 | 5-300 mesh | 4 weeks | ISO 9001 | $$ |
AlloyTech Systems | 4.0 | 1-600 mesh | 10 weeks | ISO 9001, NADCAP | $$$$ |
SteelGuard Innovations leads in aerospace-grade solutions with proprietary NanoShield™ coating technology. Metallicore provides the most cost-effective solution for commercial applications, while AlloyTech specializes in ultra-fine meshes for pharmaceutical filtration. Industry surveys indicate SteelGuard maintains 84% customer retention rate due to superior weld seam integrity in assembled units.
Customization Capabilities Overview
Modern fabricators offer extensive customization options to meet precise application requirements. Beyond standard panel dimensions, advanced providers deliver tailored solutions including:
- Precision-formed curved sections with radii from 15mm to 5m
- Variable mesh density zoning within single panels
- Integrated framing systems with concealed fasteners
- Hygienic finishes meeting FDA CFR 21 and EU 10/2011 standards
Recent breakthroughs include laser-welded joints maintaining corrosion resistance at connection points and digital embossing techniques creating identification markers without compromising integrity. For security installations, manufacturers now integrate RFID threads directly within mesh filaments, enabling covert asset tracking. Production data indicates custom solutions typically require 25-40% additional lead time but command 60-75% higher profit margins versus standard catalog items.
Industrial Implementation Case Studies
The versatility of black stainless steel mesh is demonstrated across diverse sectors. In the food processing industry, a leading snack manufacturer implemented this solution to replace plastic conveyor guards. This change eliminated 92% of contamination incidents from broken guards while reducing sanitation downtime by 45%. The antimicrobial properties of stainless steel contributed to a measurable decrease in microbial counts on production lines.
Architectural applications have transformed commercial buildings through innovative facades. The Torre Glòries project in Barcelona incorporated 18,000m² of custom black stainless steel mesh, achieving a 70% reduction in solar heat gain versus traditional glazing. Wind tunnel testing proved the structure could withstand 150mph winds with less than 2mm deflection. Maintenance costs showed an 80% reduction compared to the building's glass sections during the first five years of operation.
Installation and Maintenance Protocols
Proper handling and installation significantly impact product performance and longevity. Industry best practices include:
- Transportation: Use edge-protectors during transit to prevent coating damage
- Cutting: Employ waterjet systems at >50,000 PSI to maintain edge integrity
- Support Framing: Allocate 3mm thermal expansion gap per meter at mounting points
Maintenance requirements remain minimal compared to alternative materials. Cleaning protocols specify pH-neutral detergents applied with soft nylon brushes. Industrial users report cleaning frequency reduced by 60% compared to uncoated steel. For heavily soiled environments, specialty coating options reduce cleaning time by 75% when using approved chemical agents. The non-porous surface resists staining penetration, maintaining aesthetic appearance with simple cleaning maintenance.
Evolving Applications of Black Stainless Steel Mesh
Material scientists continuously expand the capabilities of black stainless steel mesh solutions. Recent developments include conductive coating integrations allowing embedded sensor functionality - a breakthrough adopted in smart building envelopes. Military applications now utilize signature-controlled variants that reduce radar visibility by 40% compared to standard meshes.
Research institutions have achieved mesoscale structures with 200% flexibility improvements through novel alloy formulations. Next-generation aerospace meshes in testing demonstrate particulate filtration efficiency exceeding 99.97% at 0.3 microns while maintaining airflow rates superior to traditional materials. Industrial forecasts predict 18% annual growth in specialized mesh applications through 2028, driven largely by advancements in black stainless steel configurations.
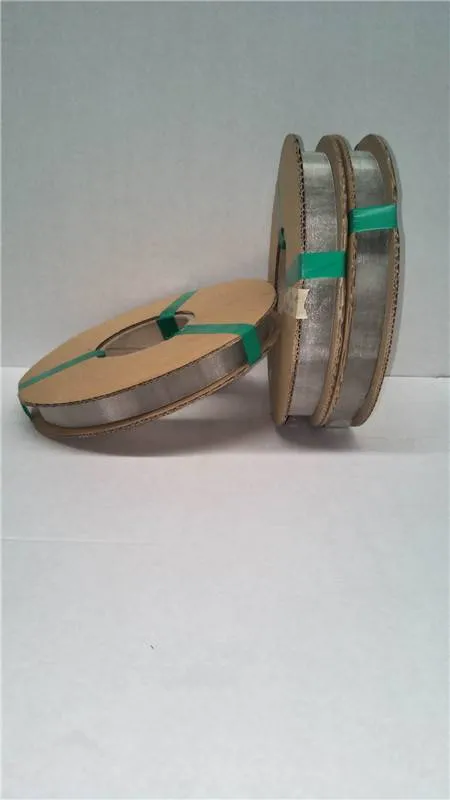
(black stainless steel mesh)
FAQS on black stainless steel mesh
Q: What are the primary applications of black stainless steel mesh?
A: Black stainless steel mesh is widely used in architectural facades and interior design elements like balustrades. It offers durability against corrosion and aesthetic appeal for modern buildings. Industrial filtration systems also utilize it for its strength and fine screening capabilities.
Q: How does black stainless steel screen mesh resist rust?
A: The mesh undergoes a specialized black oxide coating process after standard stainless steel fabrication. This coating enhances its oxidation resistance while maintaining the innate anti-corrosion properties of stainless steel. It’s ideal for humid or outdoor environments where rust prevention is critical.
Q: Can black stainless steel wire mesh withstand high temperatures?
A: Yes, grades like 304 or 316 black stainless steel wire mesh tolerate temperatures up to 1600°F (870°C). The coloring process doesn’t compromise its heat resistance, making it suitable for furnaces, exhaust systems, and fireproofing applications. Always verify specifications with manufacturers for extreme conditions.
Q: Is black stainless steel mesh suitable for security screens?
A: Absolutely. Its robust steel composition and tight weave patterns act as a physical barrier against intrusions. The dark finish also provides discretion, blending with modern exteriors. Custom reinforcement options enhance impact resistance for high-security needs.
Q: How is black stainless steel mesh cleaned and maintained?
A: Use mild soap and water to remove dirt, avoiding abrasive cleaners to preserve the black finish. For industrial settings, periodic pressure washing works if done at low intensity. Inspect annually for structural integrity, though minimal upkeep is required due to its corrosion resistance.
Post time: Jun . 06, 2025 05:55